Introduction
Heat sinks have become an important part of mechanical or electrical products. These products can range from the tiniest sizes to huge-sized machinery. As you know that there are different industries using heat sinks and some of those industries are automotive, spacecraft, computers, manufacturing industries, and much more. This article will focus on the use of heat sinks in the automotive industry. You should know that heat sinks are heat exchangers that help to transfer heat from the device to the outer environment. Just like the market for computers and other technologies is increasing, the demand for heat sinks is also increasing with time.
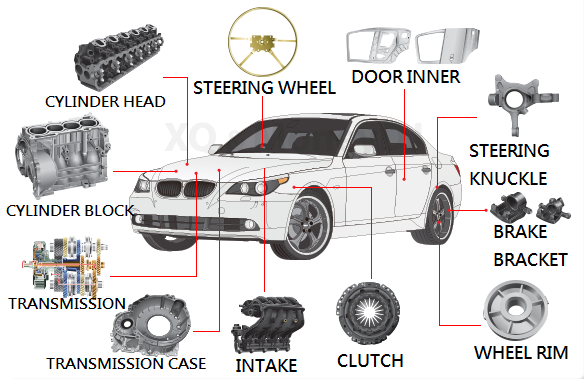
The automotive industry is also making revolutionary progress with time. Car sharing, autonomous driving, and electric vehicles are the megatrends in the automotive industry. New innovations and the latest models are radically revamping the automotive industry. An automotive includes more than 30,000 parts that can have varying functions.
The availability of thousands of parts also makes the thermal management process occur. The heat produced through the thermal management process should be dissipated properly. For the dissipation of heat, it is necessary to choose the right heat sink. Some most common heat sinks are explained under, continue reading!
What Heat Sinks Used in Automotive Industry?
Heat sinks solutions are implemented into the automotive industry based on the requirements of your vehicles. You have to keep in mind several possible factors such as the performance of your vehicles, driving time, total heat produced, speed, and much more. For example, if you drive a car at higher speeds, its engine gets warmed. As a result, more heat is produced.
To dissipate the produced heat, you need to have an efficient thermal management system. You should choose a heat sink according to all these requirements of your car. Now suppose your car doesn’t have a proper heat sink, and it will result in stopping your car.
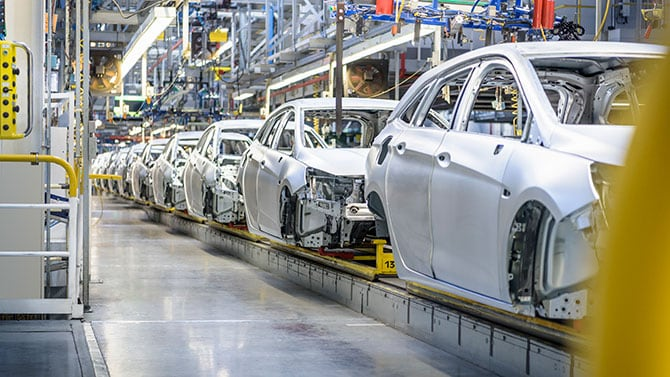
Now, let’s take an example of an electric vehicle. The thermal management systems in electric vehicles consist of transmission systems, batteries, engine cooling, and power electronics to ventilated seats. In the end, it also includes waste heat recovery for better thermal management.
It is observed that the battery acts as a main source of heat in electric vehicles. Moreover, an EV battery acts like an FSW (Friction Stir Welding). At that point, cold plate heats sinks are helpful to solve the issue. Now let’s move on to know both of these concepts:
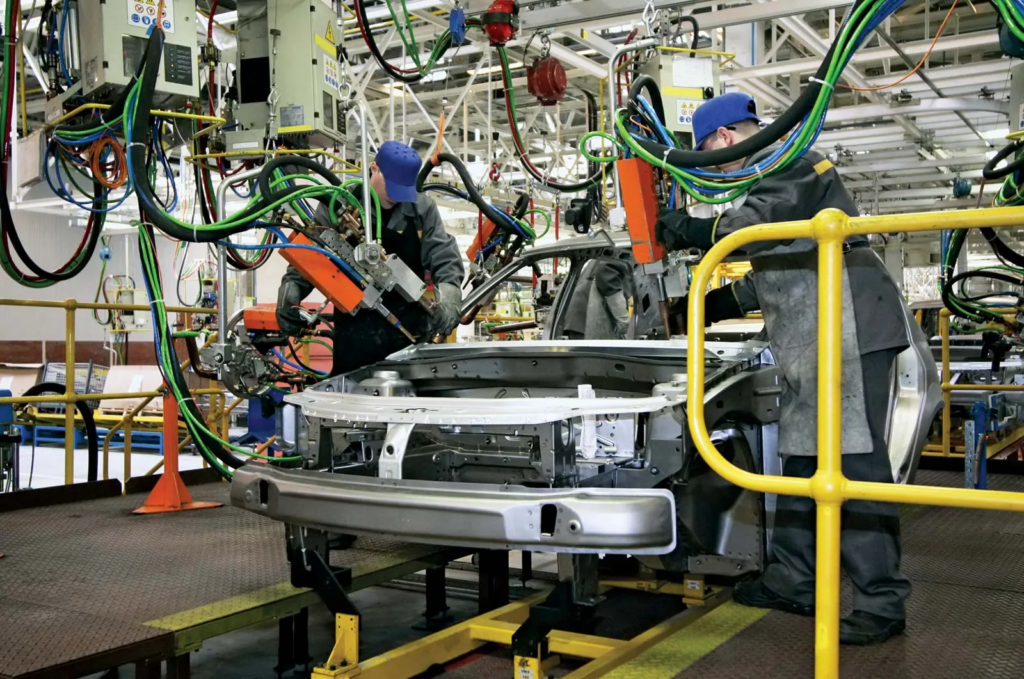
Friction Stir Welding
The friction stir welding process is mostly used for electric vehicle batteries. Moreover, this method is used especially when aluminum material is used. It makes use of a pin tool to join two materials through the help of a solid joining process. The rotating shoulder of friction stir welding produces friction heat. As a result, the produced heat softens the edges of the materials to a plastic state.
Cold Plate Heat Sinks
Cold plate heat sinks are also popular types of heat sinks used in the automotive industry. These types of heat sinks are known to be the best thermal solutions for power electronics, engine control units, and batteries. Cold plate heat sinks consist of tubes, pipes, or heat paths to the heat sinks. It also consists of a flowing liquid.
The flowing liquids help in absorbing the heat in a cycled process. The whole process consists of multiple steps such as evaporating, adiabatic process, transportation, and condensation. The main aim of the whole process is to ensure supreme thermal conductivity in your device. At the same time, it also ensures a long lifetime, high stability, and flexible channel design.
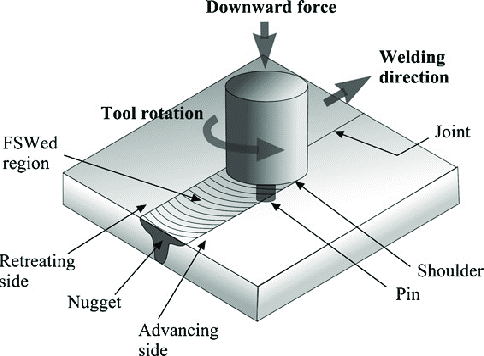
When promoting the highly qualified design of heat sinks, it is also made sure that the equipment is operating properly under recommended temperatures. The recommended temperatures are finalized based on the nature of high-power consumption devices.
Notice that the whole system works in a way that the flowing liquid transfers liquid to another cooling liquid. The liquid flow paths are machined inside the cold plate heat sinks. As these plates receive the heat, they tend to dissipate heat using the machine’s paths.
Die Casting Heat Sinks
You should know that different parts of the car use different types of heat sinks. The manufacturer implements heat sinks that work perfectly for a particular part. For example, battery housings, LED headlights, transmission systems, car stereos, and other such products use die-casting heat sinks. You should know that die-cast heat sinks are best for small devices.
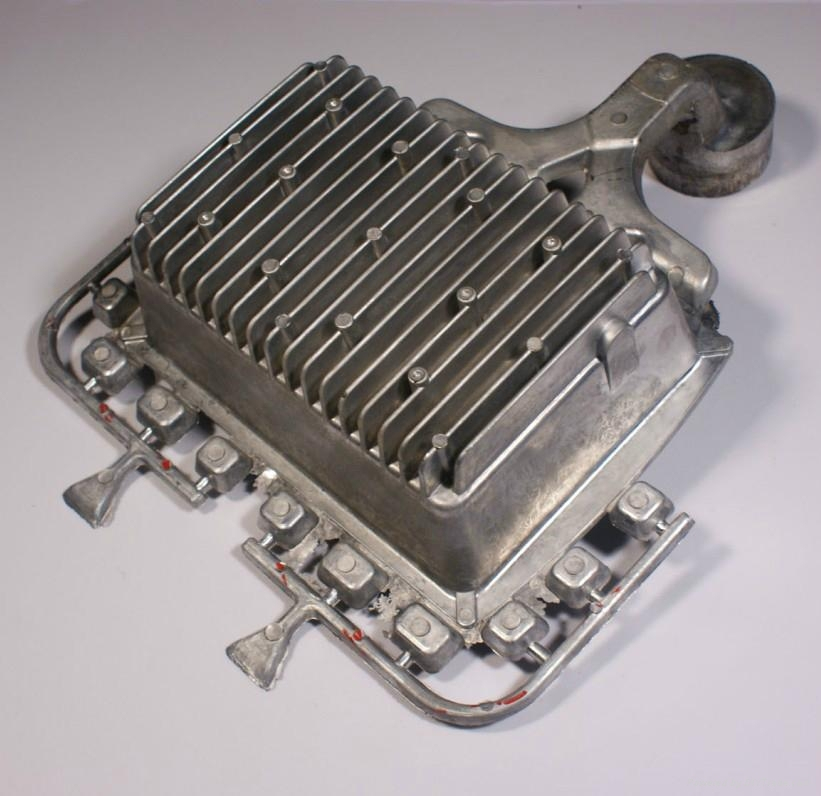
Die casting helps you to produce heat sinks with mass output and consume a very short time period. Die cast heat sinks are known for their lightweight and supreme efficiency. Due to its amazing features and properties, you can find its best uses in the automotive industry. You can also see its uses in the engine of different automotives.
You can get a custom design of die cast heat sinks at very affordable prices. Implementing these heat sinks in automotives is considered as most cost-efficient decision.
The best thing about die-cast heat sinks is that they have higher design flexibility. Therefore, more and more companies are betting on die-casting heat sinks to earn profit and manufacture efficient automotives. In simple words, you can attain temperature balance in high-density components of your automotives using die-casting heat sinks.
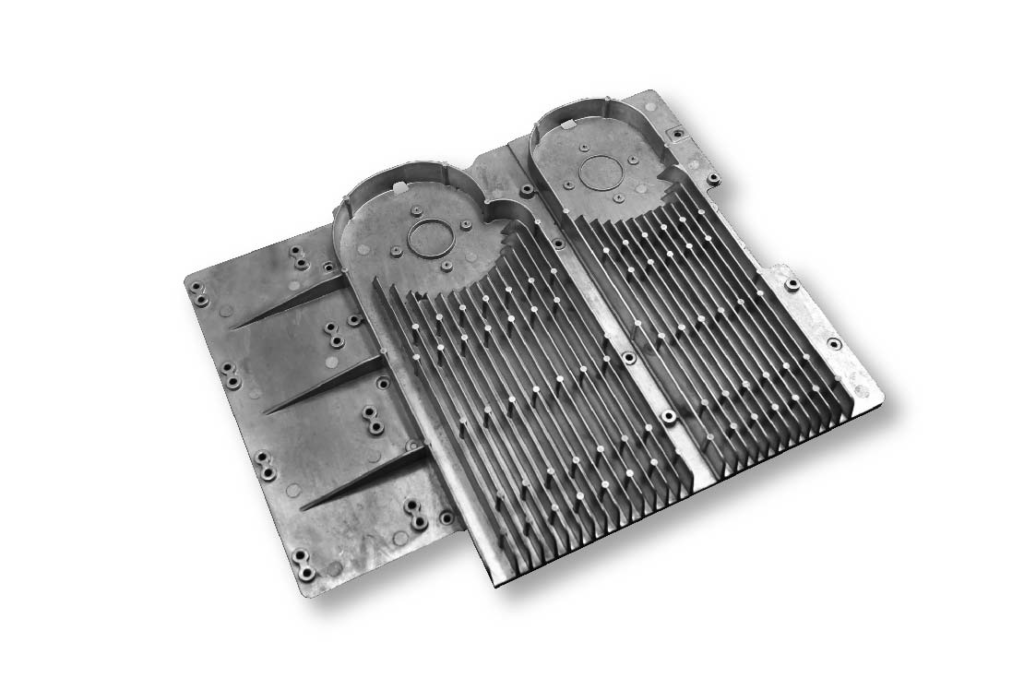
Apart from die-casting heat sinks, forged heat sinks have also become a trend in the automotive industry. Let’s explore them in detail:
Forged Heat Sinks
Forged heat sinks are manufactured using molds. A particular type of material is inserted inside the mold that you need to press with higher pressures. Forged heat sinks are also known as cold forging heat sinks. The best features of forged heat sinks are the presence of flexibility for a high aspect ratio of any type of fin. Moreover, it possesses a reliable structure.
It also offers a strong surface and accurate dimension. The materials used for forging heat sinks may vary depending on the manufacturer. The most common materials used for forged heat sins are copper and aluminum. Forged heat sinks are mostly used in gears and LED headlights.
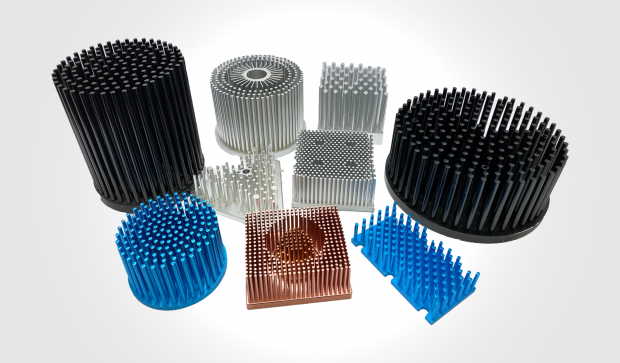
In other words, forging heat sinks involves using amazing compressive forces to improve their performance of heat sinks. Using one set of forging die, you can design forged heat sinks of different designs. When there are dense fins or high aspect ratio, forged heat sinks also possess no thermal interface between the pins or fins.
If your forged heat sink in an automotive is manufactured using aluminum then you can also insert copper chips. Doing this technique can help to improve the performance of heat sinks and hence the performance of the automotive.
Conclusion
The automotive industry is revolutionizing in different aspects. Different vehicles are being invented every single day. Each of those vehicles consists of multiple features, pros, and cons. Such a large scope of the invention is also increasing the demand for heat sinks in those vehicles.
Without a heat sink, a vehicle may not perform well due to high heat production and not being able to control it. So, are you ready to invest in high-quality heat sinks for your automotive industry? Contact Us now. We can give you custom designs of your heat sinks.