Liquid Cooling Plate For High Power Thermal Solution
- Multi-process welding processes (high-frequency welding, flame welding, brazing and friction stir welding) are available for all types of water-cooled plates
- High precision machining center to meet the production of various types of products
- Automatic three-dimensional inspection equipment to ensure that product dimensions meet the requirements of the drawings
- Highly sophisticated nitrogen and helium testing equipment to ensure no risk of product leakage
- Specialized flow resistance testing equipment to ensure product flow channel stability
- Dedicated water-cooled test platform to ensure that the thermal performance of the product meets the requirements
We will assign a sales from China, USA or Singapore, wherever is near you, to get in touch with you.
Design Service
- Icepak, ansys, EFD, Flotherm for thermal design
- Computer Aided Design (CAD) and PROE for structure design
- Weight reduction
- Eliminate fans for a passive solution
- Projected cost of the final product
Prototype And Testing
- Rapid prototype build
- CMM and precision measuring tools
- Thermal measurement devices
- Thermal chambers
- Shock testing and cycling
- Salt spray testing for corrosion analysis
Serial Order Production
- State of the art machinery
- Strict quality control
- Latest production techniques
- Focus on continuous improvement
- Robust packaging design
Pioneer Thermal have designed 3000+ projects, built 22M+ parts
Pioneer Thermal offers below liquid cooling plate process:
- Tunnel brazed
- Vacuum brazed
- Friction stir welding (maximum dimension: length 2000mm* width 1000mm*thickness 25mm
- Tube embedded
- Gun drilled
Material And Surface Treament
Materials We Work With Liquid Cooling Plate
- CU1100
- CU1020
- AL6061
- AL6063
- AL1050
- AL1060
- AL1070
- AL3003
- ADC12
- AC44300
- AC46000
- Stainless steel tube
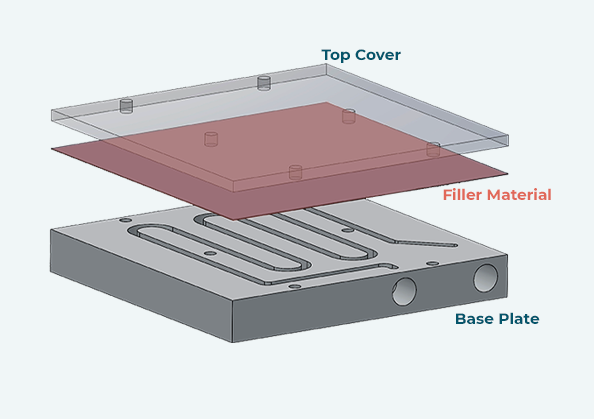
Surface Finish Available For Liquid Cold Plate
- Degrease
- Chromate
- Anodize
- Passivation
Inspection Process

Incoming Inspection
Inspect grade, dimension and cosmetic of the raw materials to ensure that the material meets the specifications.
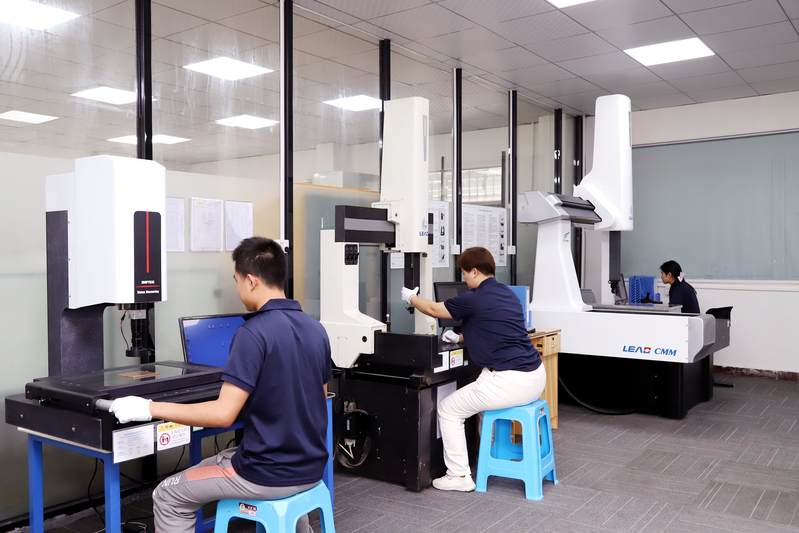
In-Process Inspection
First article inspection and AQL is performed by CMM, projector, height gauge, calliper, film tester, roughness tester etc., to verify that the heat sink meets all dimensional requirements and to ensure that it has a smooth surface finish.
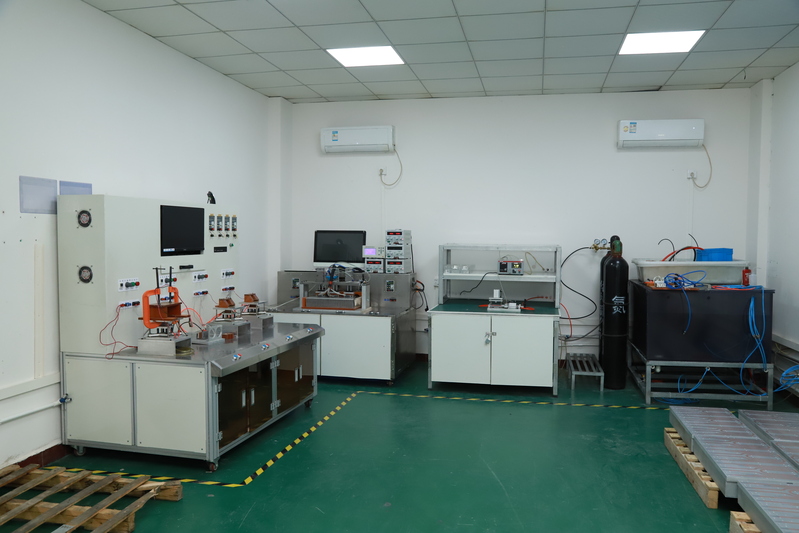
Finished Product Inspection
100% high pressure leakage test
Low pressure micro-leakage test
Flow resistance test
Flow channel cleaning
Flow channel drying
Dimension inspection
Thermal performance test

Out-Going Inspection
Cosmetic Inspection
Drop Test
Vibration Test
Label information
Why Us
As a leading supplier of liquid cold plates in China, Pioneer Thermal offers a wide range of options to meet the needs of our customers, and is committed to providing the highest quality products and services.
- We have state-of-the-art equipment and a team of highly skilled professionals who has extensive experience in designing and manufacturing high-performance liquid cold plates. We understand the importance of reliable cooling solutions, and our aim is to provide our customers with products that they can rely on. Our cold plates are designed for a wide range of applications, and we offer a variety of customization options to ensure that our products meet your specific needs. We are constantly expanding our product offerings to ensure that we can provide the best possible solutions for our customers’ needs.
- We are committed to quality. At Pioneer Thermal, we take pride in our ability to provide our customers with high-quality liquid cold plates. We operate our business in accordance with ISO 9001:2008, ISO14001:2015 & IATF16949 standards, and all of our products are backed by a 99% satisfaction guarantee.
- We offer outstanding customer service. At Pioneer Thermal, we pride ourselves on providing outstanding customer service. Our team of experts is available to answer any questions you may have and help you select the best product for your application.
- We offer competitive pricing and quick lead time. Each process is done in-house to save your cost and make fast delivery.
Whether you need a standard or custom design, Pioneer Thermal is your one-stop-shop for all your liquid cold plate needs. Contact us today to learn more about our products and services.
Liquid Cold Plate
A liquid cold plate is a device used to cool electronic components and remove unwanted heat. They work by circulating a coolant through a flat, metal plate in order to transfer heat away from the device, as the coolant circulates, it absorbs heat from the components, thereby keeping them cool.
Liquid cooling plates are typically made from copper or aluminum, which are excellent conductors of heat. The coolant used in liquid cold plates is typically a water/glycol mixture, which has a high specific heat capacity and can dissipate large amounts of heat. Liquid cold plates are used in a variety of applications, including computers, lasers, and telecommunications equipment.
Why Liquid Cold Plate?
When natural cooling and air cooling are unable to meet the heat dissipation requirement, water-cooled cooling has become the direction of choice. By circulating a coolant through a network of channels, water cooled heat sink can quickly remove heat from sensitive components. This helps to prolong the lifespan of the components and prevent overheating. In addition, water cooled heat sink are more effective than air cooling methods, making them ideal for applications where space is limited or airflow is restricted.
The original water-cooled cooling plates are more expensive, the process is also more complex, so the use of water-cooled heat sink range is not very wide. However, with the development of technology, especially the maturity of the cooling manufacturing process, the cost of water-cooled cold plates have reduced. In addition, as the product design becomes more sophisticated, liquid cold plates undoubtedly has unparalleled advantages over other cooling methods in terms of thermal performance, and is therefore valued by thermal design engineers. When properly designed and installed, liquid cold plates can provide reliable cooling performance for years to come.
Liquid Cooling Plate Types
There are six main types of liquid cooling plate:
- Friction Stir Welded (FSW) cold plate
- Vacuum Brazed liquid cooling plate
- Tube Embedded water cooling heat sinks
- Die Cast liquid water cooling heat sinks
- Extruded Liquid cooling heat sinks
- Gun Drilled Liquid water cooling heat sinks
You can check out the details via this link. Pioneer Thermal can offer above cold plates with OEM and ODM service, contact us today to find out the right solution for you.
Liquid Cooling Plate Advantages
Liquid cold plates are special types of heat exchangers. As the name implies, they use a liquid rather than air to remove heat from electronic components. There are a number of advantages to using liquid cold plates, especially for high-powered components that generate a lot of heat.
- Liquids have a much higher heat capacity than air, so they can remove more heat from the component.
- Liquids have a much higher thermal conductivity than air, so they can more efficiently transfer heat away from the component.
- By using a closed-loop system, the liquid can be circulated and cooled by a chiller or other external cooling device, making it possible to maintain a very low temperature.
- The size and weight of liquid cold plates is often smaller than air-cooled systems because there is no need for large fans or ductwork.
- Liquid cold plates will avoid icing problems by using antifreeze ethylene glycol and water and Propylene Glycol and Water (PGW) when dealing with low temperature environments
- Liquid cold plates offer the potential for increases the length of the cooling circuit path to enhance the cooling capacity, usually the circuit flow rate is controlled below 3m/s to ensure the long-term operation of the water cooling system
Custom Heat Sink Manufacturer
If you are looking a custom heat sink manufacturer, then Pioneer Thermal is your right choice. We cover all the heat sink manufacturing process, with the industry-leading equipment and mature production line in house, we are able to provide top quality custom heat sink and meantime save your cost.
In addition, our experts always give manufacture suggestions when checking your drawing, or help to create a new design to suit your application.
Main Processes
- Extrusion
- Bonded Fins
- Skived Fins
- Snapped Fins
- Folded Fins
- Heat Pipes
- Cold Forge
- Die Cast
- Friction Stir Welding Cold Plate
- Gun Drill Cold Plate
- Vacuum Brazing Cold Plate
- Vapor Chamber
Finishing Processes
- CNC machining
- Stamping
- Drilling
- Tapping
- Screen Printing
- Anodizing
- Powder Coating
- Electrophoresis
- E-coating
- Chromate
- Passivation
- Laser Etching
- Polishing
Finishing Value Added
- Embedded fans
- Thermal Grease
- Phase Change Materials
- Gap Filler Pads
- Screws
- Springs
- Clips
- Embedded Heat Pipes
- Back Plates
- PEMs
- Standoffs
- Dielectric pads
- Compounds
We'd Love To Hear From You
Hi partner, no matter you need new design & simulation for your new project, or you need heat sink manufacturing service for current on-going project, we are at your service.
What You Get When You Send Inquiry
- Less than 12 hours response to your message
- Professional advice on manufacturing process
- Seasoned design engineer help you to design a heat sink tailored to your needs
- Mature production line to save your cost
- Seamless communication to save your time
- A one-stop partner to make your work easier
You can always send inquiry with drawing to mia@ptheatsink.com