Introduction
Are you familiar with die-cast heat sinks or you are planning to purchase it? If the answer is yes, then you should read this article. This article is a helpful guide about die-cast heat sinks including their advantages, process, applications, and much more. Surprised? Auh. Let’s dig into this article.
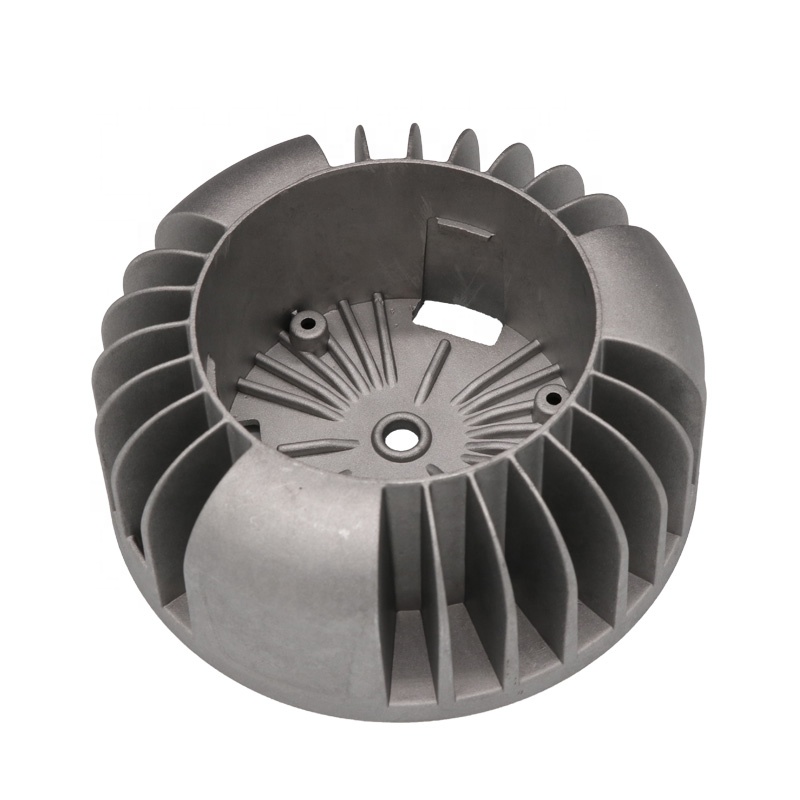
What Is Die Cast Heat Sink?
Die cast heat sinks is made from die casting process that involves pressurizing the molten metal into die cast tooling and resulting a certain shape. It’s very suitable for mass production because of the high efficiency but cheap price.
Die cast heat sink functions with another pre-designed component to keep that component cool. It aims to enhance the functions and performance of the design attached to it.
When electrical or mechanical equipment is designed, it produces heat. If the produced heat is not eliminated efficiently, it can affect the performance of your equipment.
Heat sinks are available in multiple sizes and types. Die casting heat sink is one of those types to keep your device cool. Die casting heat sinks consist of fins and is common for high-volume sales at cheaper prices. Die cast heat sinks have unique weight requirements and shapes.
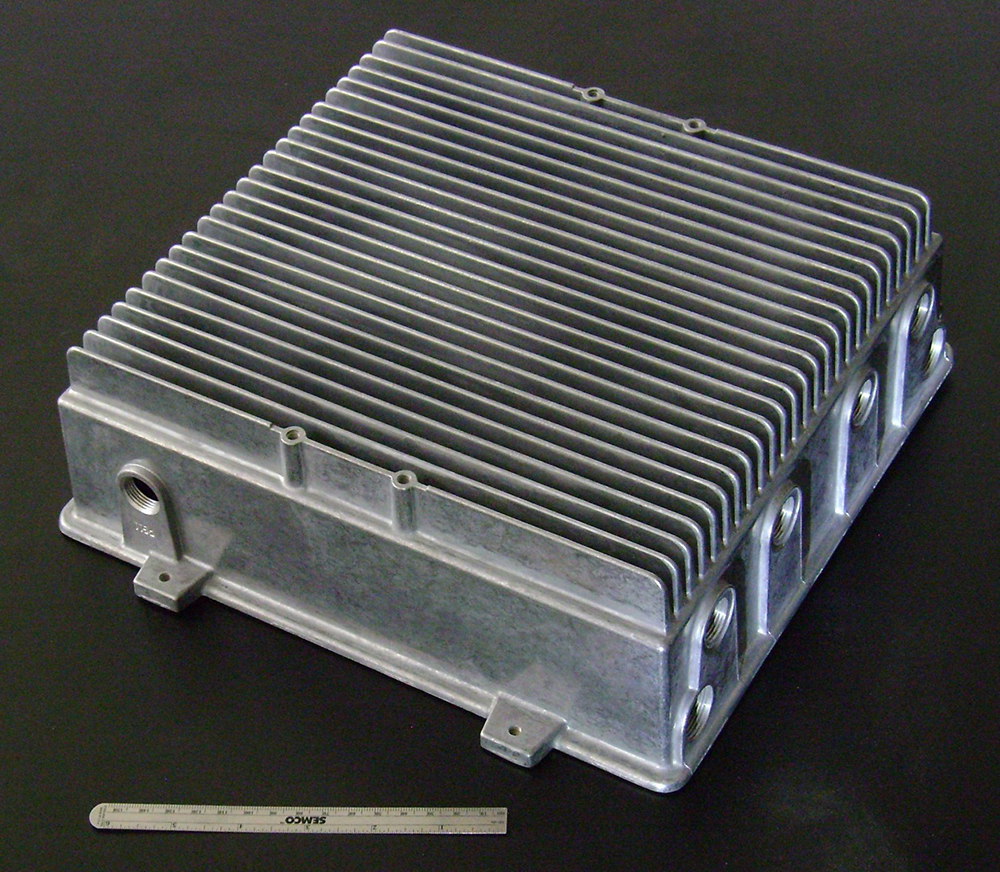
How Does Die Cast Heat Sink Work?
It is a common fact that there are different types of heat activities inside an electrical or mechanical device.
The produced heat can be due to many resources and one common source is friction. Just like many other heat sinks, die-cast heat sinks also prevent the accumulation of heat inside the device. It results in increasing the lifespan of your heat sinks.
- Die cast heat sinks are used to eliminate the heat produced by your system.
- Heat can move through the die-cast heat sinks either through the active method or the passive method. Sometimes, heat pipes are attached to die-cast heat sinks to dissipate the heat quickly.
- Heat moved from the device to the die-cast heat sink, and passes through the fins. If the die-cast heat sink is made of aluminum, there will be a smooth flow of heat.
- Slowly, the heat moves through the die-cast heat sink fins and makes the device cooler.
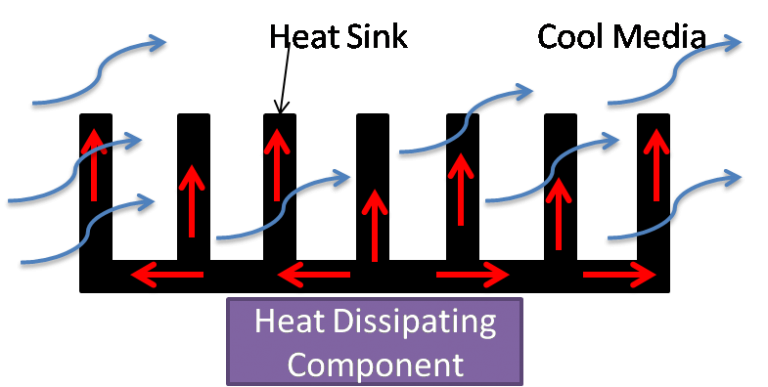
Die-Cast Heat Sink Process
- You have to create a die mold.
- Then, you have to perform lubrication on that die.
- You have to fill the die with molten metal.
- Ejection takes place from the cover die half.
- The ejector die half will produce shakeouts
- Grinding and trimming of excess materials
- Anodize, paint, or powder coat the final die-cast heat sink. Your product is ready for heat transfer.
- Note that these heat sinks are not machined heat sinks.
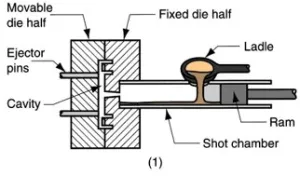
Do Die Cast Heat Sinks Have Fins?
Fins are an important part of die-cast heat sink setups to transfer heat. They help to dissipate heat efficiently out of your electrical or mechanical devices. Die cast heat sinks’ fins are more like narrow plates. These narrow plates help to dissipate the heat from a hotter environment to a cooler environment. Heat enters through one side of your fins, gets mixed with fluid, and leaves from another side. Fins continue to decrease the heat of your device’s components. There is an important role of spaces between the fins of heat sinks. If there is low space between fins, slow cooling will take place. On the other hand, wider space corresponds to the fast cooling of your device.

Advantages Of Die Cast Heat Sink
The advantages or disadvantages of a die-cast heat sink depending on the type of materials from which it is manufactured. For example, aluminum is the most used material to produce die-cast heat sinks. Some major advantages of die-cast heat sinks are listed below:
- First of all, you should notice that die-cast heat sinks work more efficiently for electrical devices.
- Die cast heat sinks involve the casting process, hence, they can exist in large varieties.
- Fins of die-cast heat sinks may exist in different spaces, shapes, and sizes.
- There are reduced complexities in die-cast heat sink designs. As a result, there is a reduced need to perform machining.
- You can add different channels to dissipate heat from the die-cast heat sink.
- Die cast heat sinks are cheaper and can be sold in large volumes.
- You can have multiple product orientations in die-cast heat sinks. No matter what the orientation of components is, heat flow is maintained properly.
- Manufacturers can also customize die-cast heat sinks according to your requirements.
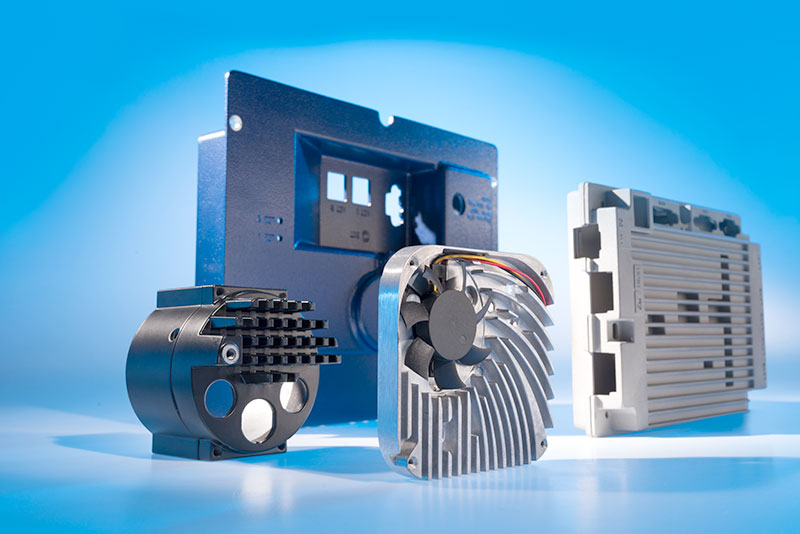
Applications Of Die Cast Heat Sink
Die cast heat sinks are popular due to their vast applications especially when they are manufactured from aluminum. Some most common applications of die-cast heat sinks are listed below:
- Laser equipment
- LED lighting
- Audio
- Automotive
- Telecom
- Automobiles
Die cast heat sinks have extending applications due to their even and vertical cooling. The best part is that you can create an electronically controlled device to produce a die-cast heat sink. You can also ask your manufacturer to design a heat sink according to the application or requirements of your device.
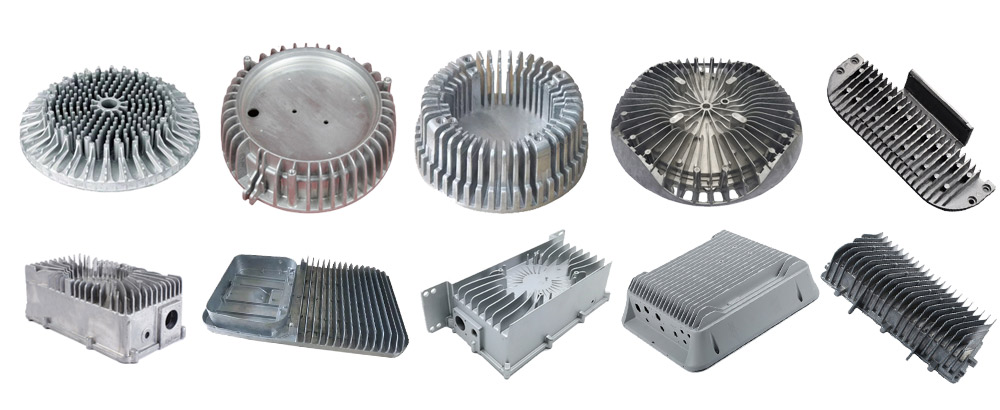
What materials Are Used to Manufacture a Die Cast Heat Sink?
As you know that there are several materials used for manufacturing die-cast heat sinks. However, manufacturers can use multiple materials to produce a high-quality heat sink for different applications. Some most common materials used to manufacture a die-cast heat sink are given below:
Aluminum Alloy
Aluminum Alloy are most widely used these days due to their cheaper prices.
Heat sink aluminum also contains good thermal conductivity but is not better than copper in heat dissipation. If you are looking for a cheaper option with higher electrical conduction aluminum, then you should buy aluminum die-cast heat sinks.
Zinc Alloy
Zinc alloy has low melting point, good fluidity and corrosion resistance, and the residual material is easy to recycle
Magnesium alloy
Small density (about 1.8g/cm3), high strength, good heat dissipation, greater ability to withstand impact loads than aluminum alloys, and good corrosion resistance to organic materials and alkalis.
Copper
Copper is known for its higher thermal conductivity in the die-cast heat sinks market. However, the price is higher and tooling life is short.
Brass
Brass is a cheaper material compared to copper and aluminum. However, it has lower thermal conductivity when compared with the other two materials.
Can You Increase the Heat Absorbing Capacity of a Die Cast Heat Sink?
Yes. It is possible to increase the heat absorbing capacity of a die-cast heat sink. For this purpose, you have to use multiple techniques that can absorb heat. As you know that the efficiency of heat sinks is highly measured by designing their fins. Now what you need to do is that you have to apply different techniques to your heat sinks’ fins.
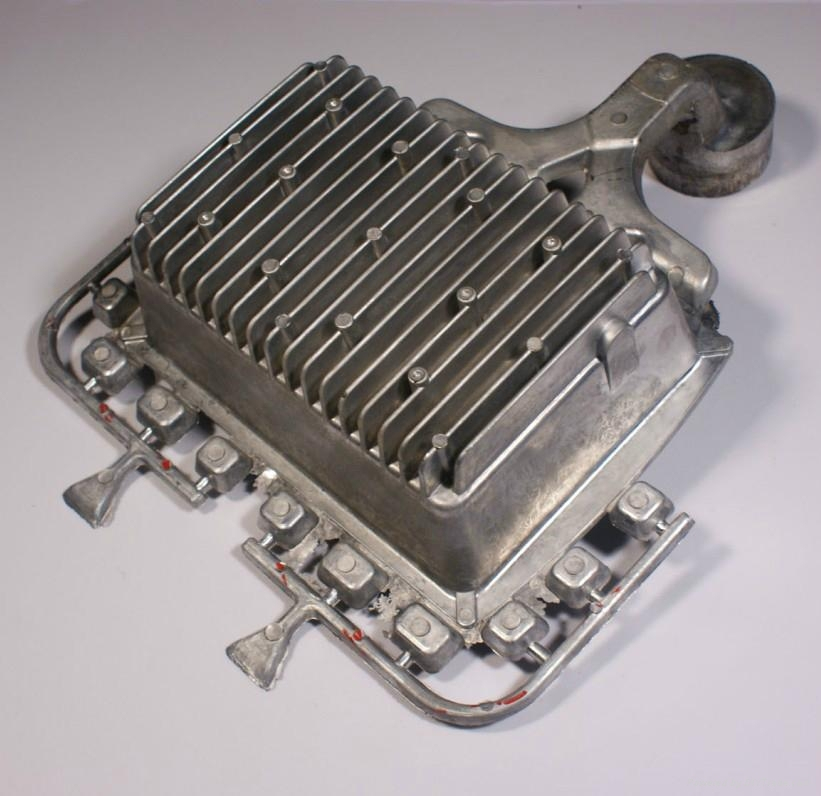
Conclusion
Die cast heat sinks are the most efficient and popular type of heat sink available in the market. Before choosing the die-cast heat sink, make sure that it matches all your requirements. For this purpose, you need to convey your needs to the manufacturer. A supplier will design a heat sink for you according to your applications. Are you looking for a manufacturer to customize a die-cast heat sink for you? Contact Us now.